Spis treści
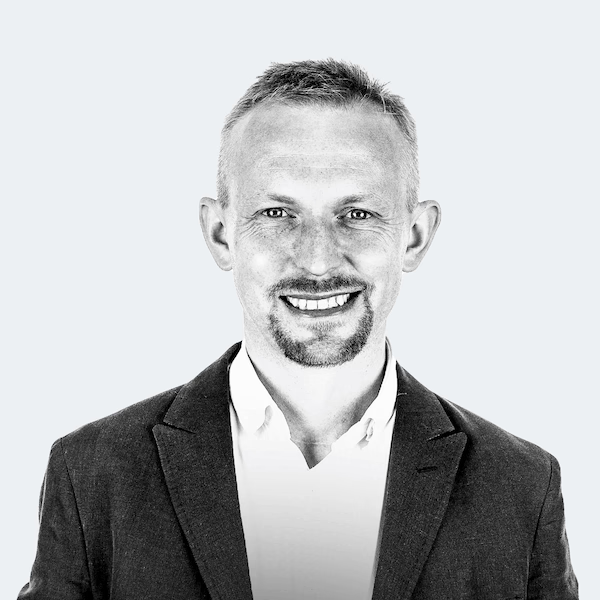
System logistyczny – co to jest i jak go stworzyć?
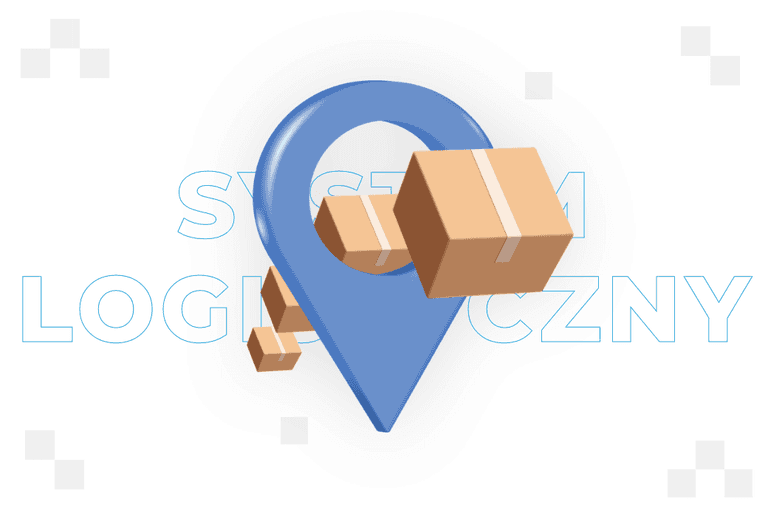
System logistyczny jest fundamentem sprawnego zarządzania łańcuchem dostaw w przedsiębiorstwie. Każdy element logistycznej układanki musi działać harmonijnie, aby zapewnić terminowość, optymalizację kosztów oraz zadowolenie klientów. Jak stworzyć skuteczny system logistyczny?
Z tego artykułu dowiesz się m.in.:
- Czym jest system logistyczny?
- Jakie są elementy systemu logistycznego?
- Jak stworzyć system logistyczny?
- Jaka jest rola systemu logistycznego?
System logistyczny – definicja
System logistyczny to kompleksowa sieć działań i procesów zaprojektowanych w celu efektywnego zarządzania przepływem towarów, informacji oraz zasobów od punktu pochodzenia do punktu końcowego konsumpcji. Obejmuje on koordynację i optymalizację wszystkich działań związanych z transportem, magazynowaniem, zarządzaniem zapasami, pakowaniem, obsługą zamówień oraz dystrybucją produktów[1] [2] [3].
System logistyczny to zintegrowane rozwiązanie zarządzające przepływem towarów, informacji i zasobów w celu optymalizacji procesów transportu, magazynowania i dystrybucji.
Definicja systemu logistycznego
Celem systemu logistycznego jest dostarczenie właściwego produktu we właściwe miejsce, we właściwym czasie, w odpowiedniej ilości i jakości, przy jednoczesnym minimalizowaniu kosztów i maksymalizowaniu efektywności operacyjnej. Działa on na różnych poziomach, w tym strategicznym, taktycznym i operacyjnym.
Elementy systemu logistycznego
System logistyczny składa się z następujących komponentów:
- Transport to główny element systemu logistycznego. Pod tym pojęciem kryje się przemieszczanie towarów od dostawców do klientów, co może odbywać się transportem drogowym, kolejowym, morskim czy lotniczym – wybór odpowiedniego środka transportu zależy od rodzaju towarów, kosztów, czasu dostawy i dostępności infrastruktury.
- Magazynowanie to przechowywanie towarów w odpowiednich warunkach do momentu ich dalszej dystrybucji. Magazyny mogą różnić się wielkością i specjalizacją, np. magazyny chłodnicze przeznaczone są dla produktów spożywczych. Zarządzanie magazynem pozwala optymalizować przestrzeń i minimalizować koszty magazynowania.
- Zarządzanie zapasami polega na kontrolowaniu poziomów zapasów, aby były stale dostępne przy jednoczesnym minimalizowaniu kosztów magazynowania i ryzyka przeterminowania. Pozwala to utrzymać równowagę między popytem i podażą.
- Pakowanie obejmuje zabezpieczenie towarów na czas transportu i magazynowania, co chroni je przed uszkodzeniami, ułatwia przenoszenie oraz zapewnia odpowiednie warunki przechowywania. Pakowanie w niektórych wypadkach musi też spełniać wymogi prawne i sanitarne.
- Obsługa zamówień obejmuje przyjmowanie, przetwarzanie i realizację zamówień od klientów. Wymaga to sprawnej komunikacji, precyzyjnego planowania i szybkiej reakcji na potrzeby klientów, ponieważ jest to ważne w utrzymaniu satysfakcji klienta i budowania długotrwałych relacji biznesowych.
- Zarządzanie informacją to gromadzenie, przetwarzanie i dystrybucję informacji niezbędnych do podejmowania decyzji logistycznych. Systemy informatyczne, takie jak systemy WMS czy ERP, umożliwiają integrację danych i automatyzację procesów logistycznych.
- Planowanie i zarządzanie przepływem dotyczy strategii i taktyk wykorzystywanych do zarządzania łańcuchem dostaw, co obejmuje planowanie tras transportowych, harmonogramowanie dostaw, optymalizację zasobów oraz zarządzanie ryzykiem. Celem jest zapewnienie płynności operacji logistycznych i minimalizacja opóźnień.
- Kontrola jakości zapewnia, że wszystkie elementy procesu logistycznego spełniają określone standardy jakości. Obejmuje monitorowanie i ocenę produktów, procesów oraz usług w celu wykrycia i eliminacji potencjalnych problemów i zapewnienia zgodności z wymaganiami klientów.
- Usługi dodatkowe mogą obejmować różne działania wspierające, takie jak serwis posprzedażowy, zwroty towarów, naprawy oraz recykling. Pomagają w budowaniu wartości dodanej dla klienta i zwiększają konkurencyjność firmy.
Tworzenie systemu logistycznego
Tworzenie systemu logistycznego wymaga starannego planowania, analizy i wdrożenia; warto w tym celu podążać według poniższego planu:
Analiza potrzeb i celów
Pierwszym krokiem jest zrozumienie, jakie produkty będą przemieszczane w systemie logistycznym. W tym celu należy określić ich rodzaje oraz zbadać ich fizyczne właściwości (wymiary, waga, wymagania dotyczące opakowań) i wszelkie wymagania dotyczące przechowywania i transportu.
Następnie należy zrozumieć oczekiwania klientów – są oni najważniejszymi interesariuszami systemu logistycznego, więc żeby system logistyczny działał prawidłowo, należy ustalić ich oczekiwania dotyczące czasu realizacji zamówień, częstotliwość zamówień i preferencje dotyczące harmonogramu dostaw. Warto też dowiedzieć się, jakie są ich oczekiwania względem jakości obsługi klienta.
Kolejnym elementem jest przewidywanie wolumenów i częstotliwości przesyłek. W tym celu należy przeanalizować dane z przeszłości, aby zidentyfikować trendy sprzedażowe, sezonowość oraz okresy szczytowego popytu. Dobrze jest też wykorzystać narzędzia analityczne do prognozowania przyszłego popytu, biorąc pod uwagę czynniki zewnętrzne, takie jak zmiany rynkowe, działania konkurencji oraz planowane kampanie marketingowe.
Następną częścią jest określenie ograniczeń budżetowych i czasowych – budżet powinien uwzględniać wszystkie koszty operacyjne, a harmonogram wdrożenia nowego systemu logistycznego powinien brać pod uwagę wszystkie etapy procesu oraz czas potrzebny na szkolenie personelu i testowanie systemu.
Na podstawie zebranych danych należy określić cele logistyczne. Najważniejsze z nich to:
- Maksymalizacja szybkości dostaw może zaspokoić potrzeby klientów.
- Minimalizacja kosztów operacyjnych może pomóc w zwiększeniu marż zysku i konkurencyjności na rynku.
- Wysoka jakość obsługi klienta buduje lojalność konsumencką i pozytywny wizerunek firmy.
- Możliwość szybkiego dostosowywania się do zmieniających się warunków rynkowych i potrzeb klientów może pomóc w dynamicznych branżach.
Badanie i ocena istniejących procesów
Szczegółowa analizy obecnych procesów logistycznych pozwala na identyfikację mocnych stron, słabych punktów oraz możliwości poprawy w istniejącym systemie. Na początku należy zbadać cały proces przepływu towarów od dostawców do klientów, czyli warto odpowiedzieć sobie na pytania:
- Jakie są procedury odbioru towarów od dostawców? Czy istnieją standardowe procedury operacyjne dla odbioru, weryfikacji ilości i jakości dostarczanych produktów?
- Jak towary są przechowywane w magazynie? Czy istnieją jasno zdefiniowane lokalizacje dla różnych produktów? Jak efektywnie wykorzystywana jest przestrzeń magazynowa?
- Jakie są procesy kompletacji zamówień? Czy istnieją standardowe procedury kompletacji, pakowania i przygotowywania towarów do wysyłki?
- Jakie są procedury wysyłki towarów do klientów? Jakie metody transportu są używane? Jak zarządzane są harmonogramy dostaw i komunikacja z przewoźnikami?
Kolejnym krokiem jest analiza zarządzania zapasami. W tym celu należy sprawdzić czynniki, takie jak poziomy i rotacja zapasów oraz metody prognozowania popytu. Jednocześnie warto sprawdzić stan i jakość procedur magazynowych pod kątem ich efektywności i zgodności z najlepszymi praktykami. W tej fazie należy zbadać, jak dobrze zarządza się przestrzenią magazynową, czy procedury magazynowe zapewniają bezpieczeństwo pracowników i minimalizują ryzyko wypadków oraz przeprowadzić audyt technologii wykorzystywanych w magazynie. Następnie można przejść do analizy transportu, która powinna zbadać m.in. kryteria wyboru przewoźników, metody optymalizacji tras i metody monitorowania przesyłek.
Dane zebrane w każdym z wymienionych wyżej elementów posłużą do przeprowadzenia całościowej analizy, która pozwoli m.in.:
- zidentyfikować najważniejsze KPI (np. czas realizacji zamówień, wskaźniki rotacji czy poziom satysfakcji klienta);
- przeprowadzić analizę SWOT dla obecnych procesów logistycznych;
- przeanalizować koszty związane z logistyką, w tym koszty transportu, magazynowania, zarządzania zapasami oraz inne koszty operacyjne.
Ostatnią częścią tej fazy jest identyfikacja obszarów, w których system logistyczny działa skutecznie, a także obszarów wymagających poprawy. Pozwoli to określić możliwości wprowadzenia innowacji, które mogą poprawić wydajność systemu – w tym celu warto też poznać opinie pracowników bezpośrednio zaangażowanych w procesy logistyczne.
Projektowanie systemu
Opracowanie koncepcji nowego systemu logistycznego wymaga m.in. starannego zaprojektowania struktur organizacyjnych. W tym wypadku najczęściej stosuje się strukturę hierarchiczną, w której poziom odpowiedzialności rośnie wraz z poziomem w hierarchii. Oznacza to, że dyrektor ds. logistyki będzie odpowiedzialny za nadzór nad całością działań logistycznych, strategię logistyczną, zarządzanie zespołem oraz współpracę z innymi działami firmy, a koordynator ds. zamówień będzie zajmował się tylko przyjmowaniem, przetwarzaniem i realizacją zamówień klientów.
System logistyczny powinien mieć również jasno zdefiniowane procesy operacyjne. Trzeba też pamiętać, że każdy proces może składać się z mniejszych podprocesów – przykładowo przyjęcie towarów najczęściej składa się z:
- sprawdzenia dokumentacji dostawy,
- przygotowania stanowisk odbioru,
- weryfikacji ilości i jakości dostarczonych towarów,
- rejestracji w systemie magazynowym,
- przypisania odpowiednich lokalizacji magazynowych,
- transportu wewnętrzny do miejsca składowania.
Poza przyjęciem towaru inne standardowe procesy operacyjne w systemach logistycznych to zarządzanie zapasami, kompletacja zamówień, transport i dystrybucja.
Poza zdefiniowaniem procesów należy też określić wymagania technologiczne systemu logistycznego i standardy jakości, które powinny budować regularne audyty, kontrole na wejściu i wyjściu oraz skuteczna strategia zarządzania zwrotami.
Ważnym elementem działania przyszłego systemu logistycznego będą scenariusze operacyjne. Każdy system powinien uwzględniać ich kilka:
- Scenariusz normalnej operacji zakłada standardowy przepływ towarów, stabilny popyt, regularne dostawy i wysyłki.
- Scenariusz szczytowego obciążenia opisuje sytuację zwiększonego popyt, np. w okresach świątecznych, co zakłada konieczność szybkiego zwiększenia zasobów.
- Scenariusz awaryjny opisuje działania w przypadku zakłóceń w dostawach czy problemów z transportem oraz powinien zawierać metody reagowanie na kryzysy.
Wybór technologii i narzędzi
Zidentyfikowanie i wybór odpowiednich technologii oraz narzędzi informatycznych to kolejny krok w projektowaniu nowego systemu logistycznego. Właściwie dobrane technologie mogą znacząco poprawić efektywność, precyzję oraz szybkość procesów logistycznych. Skutecznie działający system powinien zawierać m.in.:
- system WMS do zarządzania magazynem, lokalizacjami, automatyzacji procesów magazynowych oraz śledzenia zapasów;
- system TMS do zarządzania transportem poprzez planowanie najbardziej efektywnych tras, monitorowanie przesyłek i zarządzanie relacjami z przewoźnikami;
- system ERP do integracji i automatyzacji procesów biznesowych; może on też służyć jako centralna baza danych;
- system OMS do zarządzania całym cyklem życia zamówienia, od przyjęcia przez realizację do dostawy.
- technologie RFID (Radio Frequency Identification) umożliwiają automatyczną identyfikację i śledzenie produktów za pomocą fal radiowych;
- a także automatyczne regały, systemy składowania i sortowania oraz roboty magazynowe.
Dobierając technologie do systemu logistycznego, należy sprawdzić, jakie oprogramowanie już jest używane w firmie i upewnić się, że nowe technologie mogą być z nimi bez problemów zintegrowane. Warto też wybierać technologie oferujące solidne interfejsy API i systemy modułowe, które można rozbudowywać w miarę potrzeb firmy.
Przed sprawdzeniem systemu logistycznego w „bojowych warunkach” dobrze jest przeprowadzić pilotażowe wdrożenie wybranych technologii w jednym lub kilku działach, aby ocenić ich efektywność i wykryć potencjalne problemy. Jednocześnie należy zadbać o szkolenia dla pracowników, aby mogli skutecznie korzystać z nowych technologii i narzędzi.
Planowanie zasobów
Określenie zasobów niezbędnych do wdrożenia nowego systemu logistycznego rozpoczyna się od stworzenia zespołu projektowego. W jego skład powinni wchodzić:
- kierownik projektu, który będzie odpowiedzialny za zarządzanie projektem, koordynację działań i komunikację z interesariuszami;
- specjalista ds. IT, który będzie odpowiedzialny wybór i integrację systemów informatycznych;
- analityk biznesowy, który będzie odpowiedzialny za analizę potrzeb i wymagań biznesowych;
- menadżer ds. logistyki, który będzie odpowiedzialny za analizę i optymalizację procesów logistycznych;
- koordynator ds. szkoleń, który będzie odpowiedzialny za opracowanie i realizację programu szkoleniowego dla pracowników.
Oprócz zespołu projektowego warto też uwzględnić dodatkowy personel w rodzaju pracowników magazynu, kierowców czy specjalistów ds. obsługi klienta.
Kolejnym krokiem jest określenie budżetu. Musi on zawierać koszty początkowe (w nie wlicza się m.in. zakup technologii i szkoleń), koszty operacyjne (które obejmują m.in. utrzymanie systemów, zarządzanie personelem oraz transport), koszty infrastruktury (obejmują np. modernizację magazynów), technologii (np. zakup terminali RFID) oraz automatyzacji (np. przez zakup robotów magazynowych). Należy też określić sprzęt niezbędny do działania systemu logistycznego. Zalicza się do niego m.in. wózki widłowe, regały i systemy składowania, komputery i serwery oraz skanery i drukarki.
Wdrożenie systemu i ciągłe doskonalenie
Wdrożenie zaprojektowanego systemu logistycznego powinno być przeprowadzone etapowo, aby łatwiej można było zarządzać zmianami. Faza pierwsza to przygotowanie, które należy rozpocząć od zainstalowania i skonfigurowania wybranych wcześniej systemów oraz upewnić się, że wszystkie są zintegrowane i kompatybilne z istniejącymi rozwiązaniami. W tej fazie instaluje się też wszystkie niezbędne sprzęty, od regałów po drukarki.
Faza druga to implementacja – w jej trakcie wprowadza się nowe procedury operacyjne, po czym przeprowadza się pilotażowe wdrożenie w jednym magazynie lub sekcji, aby przetestować nowe procesy i technologie. Na tym etapie należy też przeprowadzić szkolenia dla pracowników.
Faza trzecia to testowanie i dostosowywanie. Przed pełnym uruchomieniem systemy należy przeprowadzić dokładne testy funkcjonalności systemów IT oraz nowych procesów operacyjnych, żeby znaleźć i naprawić błędy oraz dostosować działanie systemu na podstawie wyników testów i feedbacku od użytkowników. Dopiero po tym można zacząć użytkować system logistyczny.
Jednocześnie warto ustawić kamienie milowe. Przykładowo kamieniem milowym dla fazy pierwszej może być ukończenie analizy potrzeb i wyboru technologii, a dla fazy trzeciej zakończenie testowania systemów. Ważne jest, żeby kamienie milowe jasno określały, co należy osiągnąć i kiedy najpóźniej należy tego dokonać.
Po wdrożeniu systemu należy regularnie monitorować jego działanie, aby upewnić się, że spełnia ustalone cele i przynosi oczekiwane korzyści – do oceny dobrze jest wykorzystywać KPI wybrane na początku procesu. Dobrze jest też pamiętać, że system logistyczny powinien być zdolny do adaptacji do zmieniających się warunków rynkowych i technologicznych, więc warto regularnie przeprowadzać audyty systemu, aby zidentyfikować możliwości poprawy.
Rola systemu logistycznego
System logistyczny jest niezbędnym narzędziem do zarządzania przepływem towarów, informacji i zasobów w całym łańcuchu dostaw, począwszy od dostawców aż po ostatecznych klientów. Zapewnia on efektywność, terminowość i opłacalność operacji logistycznych, co bezpośrednio wpływ na satysfakcję klienta.
Skuteczny system logistyczny umożliwia m.in. optymalizację transportu, precyzyjne planowanie i prognozowanie popytu, śledzenie przesyłek w czasie rzeczywistym, co zwiększa przejrzystość operacji oraz pozwala zwiększyć wydajność operacyjną. Odgrywa on ważną rolę w zarządzaniu relacjami z dostawcami i przewoźnikami, a to pozwala lepiej koordynować działania i odpowiadać na potrzeby klientów, dzięki czemu można utrzymać konkurencyjność na rynku.
FAQ
Formularz kontaktowy
Rozwijaj swoją firmę
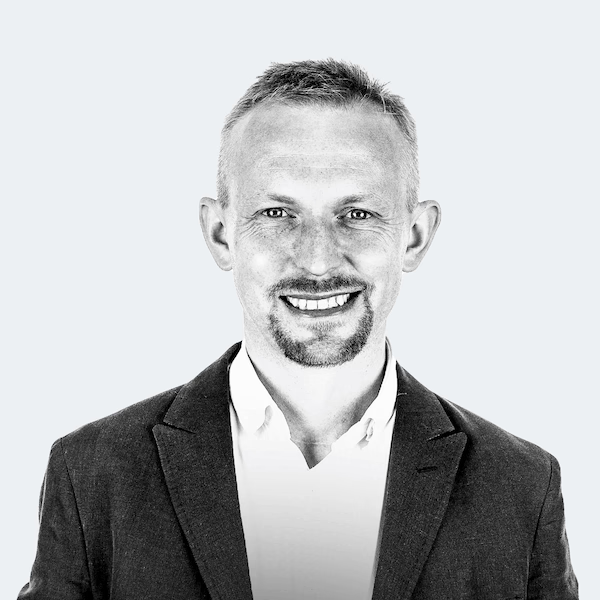
Specjalizuję się w zarządzaniu zmianą i zarządzaniu portfelem projektów. Z wykształcenia jestem inżynierem przemysłowym i uwielbiam usprawniać otoczenie. W mojej codziennej pracy koncentruję się na poszerzaniu świadomości, zaangażowaniu i wsparciu zespołu. Moje drzwi są zawsze otwarte.
Oceń tekst
Być może zainteresują Cię:
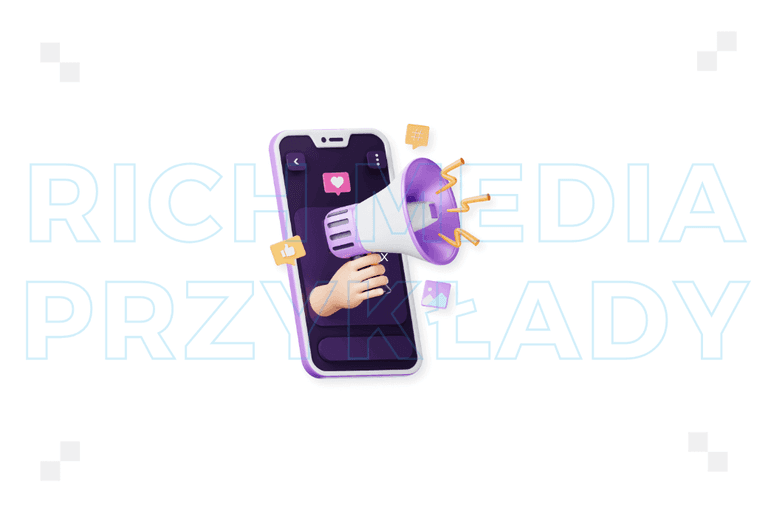
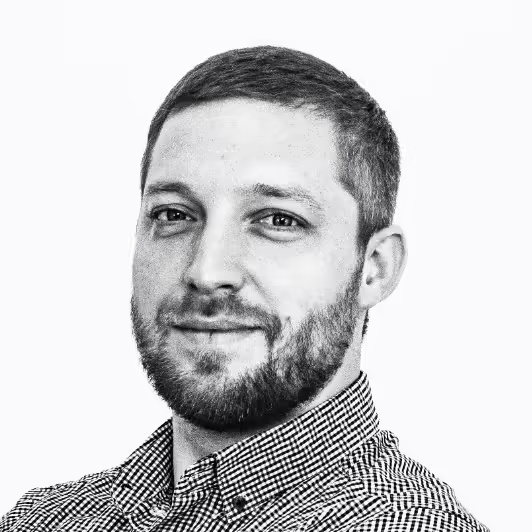
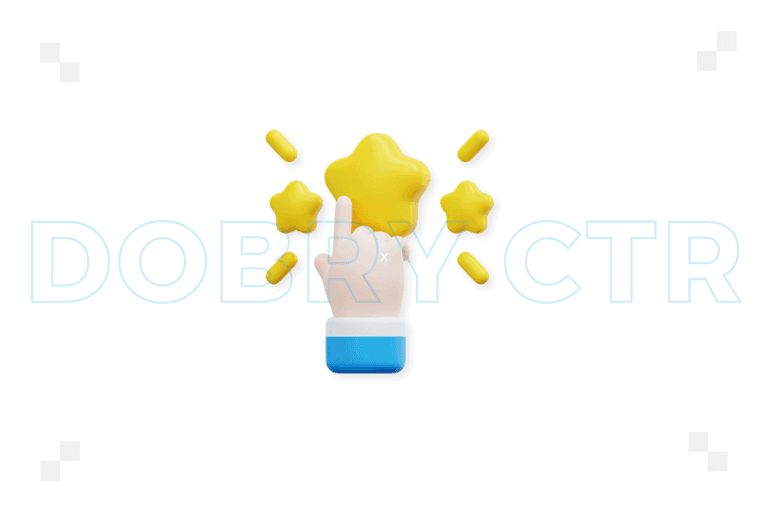
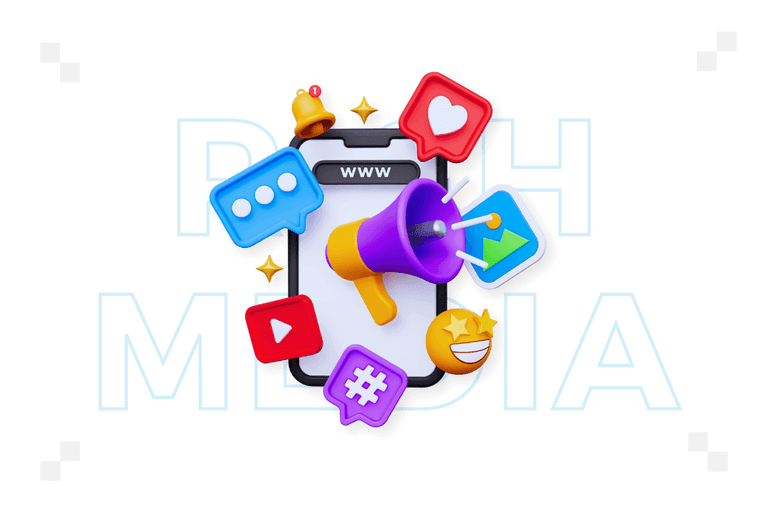