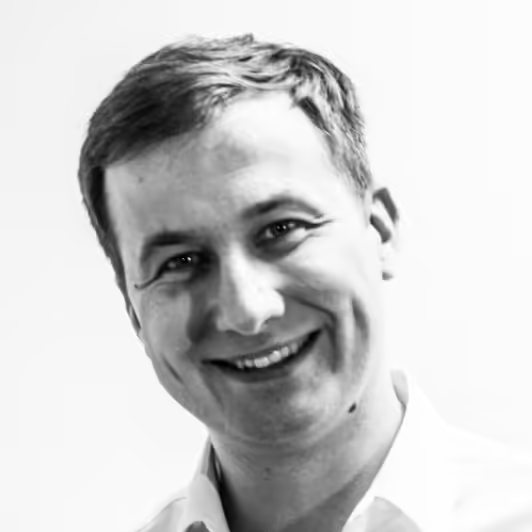
Lean management – co to jest i do czego służy?
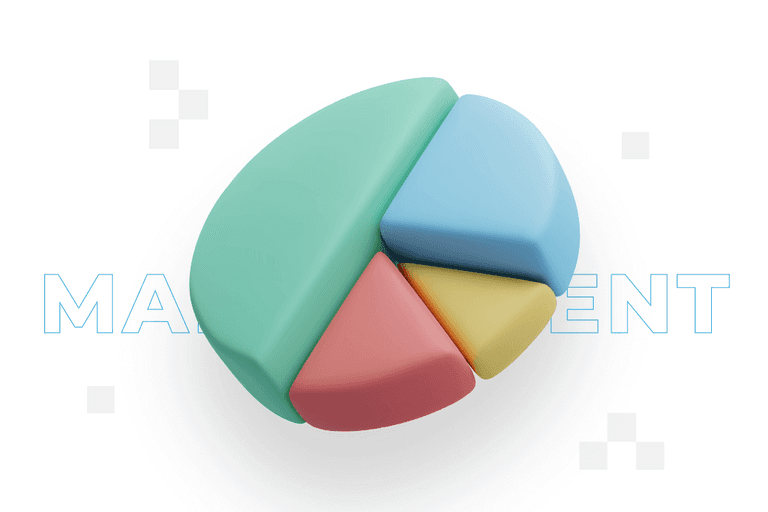
Lean management to filozofia zarządzania, która pozwala firmom zwiększyć efektywność, eliminować marnotrawstwo i dostarczać klientom większą wartość. Znajduje zastosowanie w różnych branżach – od produkcji po e-commerce i usługi. Jak dzięki jej narzędziom organizacje mogą minimalizować koszty, skracać czas realizacji i poprawiać jakość?
Z tego artykułu dowiesz się m.in.:
- Czym jest lean management?
- Jaka jest historia lean management?
- Jakie są zasady lean management?
- Jakie są narzędzia lean management?
- Jak wdrożyć lean management?
- Gdzie można stosować lean management?
- Jakie są ograniczenia lean management?
- Jakie są korzyści z lean management?
Lean management – definicja
Lean management (znane też jako lean manufacturing, lean production management, metoda lean i koncepcja szczupłego zarządzania; lean znaczy szczupły, odchudzony) to koncepcja zarządzania przedsiębiorstwem ukierunkowana na maksymalizację wartości dostarczanej klientowi przy jednoczesnej eliminacji wszystkich możliwych form marnotrawstwa.
Fundamentem koncepcji lean management jest identyfikacja działań, które przynoszą wartość z perspektywy konsumenta, oraz systematyczne eliminowanie z codziennej pracy operacji generujących straty, takich jak nadprodukcja, zbędne zapasy, zbytnie przetwarzanie, postoje czy nieefektywny transport.
Lean management to strategiczna metodyka optymalizacji działań i procesów w organizacji poprzez eliminację wszelkich form marnotrawstwa, która dąży do maksymalizacji wartości dla klienta.
Definicja lean management
Podstawą lean management jest wdrożenie metod i narzędzi pozwalających na poprawę efektywności operacyjnej, takich jak system ssący (pull system), zarządzanie wizualne, ustandaryzowanie pracy oraz Total Productive Maintenance (TPM). Szczególne znaczenie ma również podejście Kaizen, które zakłada ciągłe doskonalenie procesów poprzez angażowanie wszystkich pracowników w identyfikację i wdrażanie usprawnień.
Wdrażanie lean w organizacji wymaga nie tylko zmian w strukturze procesów, ale także kształtowania kultury organizacyjnej opartej na współpracy, odpowiedzialności i dążeniu do doskonałości operacyjnej. Skuteczność zależy od konsekwentnego stosowania zasad oraz zaangażowania kierownictwa i zespołów operacyjnych w proces transformacji lean.
Historia lean management
Jednym z pierwszych prekursorów lean production był Frederick Winslow Taylor, który pod koniec XIX i na początku XX wieku opracował zasady naukowego zarządzania (Scientific Management)[1]. Skupiał się na analizie ruchów roboczych, podziale pracy i standaryzacji procesów w celu zwiększenia wydajności.
Początków koncepcji lean management rozpoczyna się w latach 20. i 30. XX wieku – wczesne zasady tej koncepcji zaczęły krystalizować się w procesach produkcyjnych stworzonych przez firmę Ford Motor Company. Henry Ford i jego zespół wprowadzili koncepcję linii montażowej i standaryzacji pracy, co zrewolucjonizowało produkcję masową[2].
Prawdziwa rewolucja w zarządzaniu produkcją nastąpiła jednak w Japonii po II wojnie światowej, gdy Taiichi Ohno i Eiji Toyoda w Toyota Motor Corporation opracowali Toyota Production System (TPS) – system zarządzania produkcją, który stał się podstawą dla lean management[3].
System produkcyjny Toyoty koncentrował się na usuwaniu marnotrawstwa (muda), nierówności (mura) i przeciążeń (muri), wprowadzając koncepcje, takie jak Just-in-Time (JIT), system ssący (pull system) oraz autonomizacja (jidoka), która umożliwia pracownikom wykrywanie i eliminację problemów jakościowych w czasie rzeczywistym[4] [5].
W latach 70. i 80., gdy japoński przemysł motoryzacyjny zaczął dominować na globalnym rynku, System Produkcyjny Toyoty zaczął przyciągać uwagę na świecie. W tym czasie metodologie te były nadal głównie kojarzone z przemysłem motoryzacyjnym.
W 1990 roku pojęcie „lean” zostało formalnie zdefiniowane przez Jamesa P. Womacka i Daniela T. Jonesa w ich książce „The Machine That Changed the World” (napisali oni także równie słynne „Lean Thinking”)[6] [7]. Autorzy opisali zasady i praktyki TPS, promując je jako podstawowe narzędzia zarządzania, które można zastosować w różnych sektorach przemysłu.
W XXI wieku konlean management dalej ewoluował i rozprzestrzenił w różnych sektorach, od produkcji po usługi zdrowotne, finanse, budownictwo czy edukację. Lean management, choć zakorzeniony w produkcji, ewoluował w kierunku wszechstronnej filozofii zarządzania, a zasady szczupłego zarządzania są stosowane w kontekście globalnym i integrują nowoczesne podejścia takie jak metodologia Agile czy metodologia Six Sigma. Obecnie lean management jest stosowany w różnorodnych branżach, a jego ewolucja obejmuje integrację z nowoczesnymi technologiami, takimi jak Przemysł 4.0, Lean IT czy Lean Healthcare, co pokazuje jego zdolność do adaptacji do zmieniających się warunków rynkowych i technologicznych.
Zasady lean management
Oto główne zasady lean management:
Określenie wartości z perspektywy klienta
Określenie wartości z punktu widzenia klienta to fundament lean management, który pozwala organizacjom skoncentrować się na dostarczaniu produktów i usług w sposób zgodny z rzeczywistymi potrzebami odbiorców. Polega to dokładnej analizie oczekiwań klientów, ich priorytetów oraz czynników, które wpływają na ich decyzje zakupowe.
Jednym z celów lean management jest zrozumienie, co klient postrzega jako wartość – nie tylko w kontekście samego produktu czy usługi, ale także całego doświadczenia związanego z ich otrzymaniem, takich jak czas realizacji, jakość obsługi czy niezawodność dostaw, co jest ważne w procesie tworzenia wartości. W tym kontekście wartość jest definiowana jako wszystko to, za co klient jest gotów zapłacić, co oznacza, że każda operacja lub proces, który nie wnosi realnej wartości dodanej, powinien być uznany za marnotrawstwo i podlegać eliminacji lub optymalizacji.
Aby skutecznie określić wartość, organizacja powinna wykorzystywać różnorodne metody badania rynku i zachowań konsumentów, takie jak analiza danych sprzedażowych, badania satysfakcji, wywiady czy testy użytkowe. Pozwala to na uzyskanie kompleksowego obrazu preferencji klientów i dostosowanie oferty w sposób, który maksymalizuje jej atrakcyjność.
Zrozumienie wartości z perspektywy klienckiej prowadzi także do unikania nadmiernego skomplikowania produktów lub usług, które mogą zwiększać koszty i czas produkcji, ale niekoniecznie przekładają się na wyższą wartość dla odbiorcy. Minimalizacja niepotrzebnych funkcji, zmniejszenie zapasów optymalizacja kosztów produkcji oraz skrócenie czasu dostawy to najważniejsze elementy strategii lean, które pozwalają zwiększyć konkurencyjność organizacji.
Marnotrawstwo
Zminimalizowanie marnotrawstwa to jedna z najważniejszych zasad lean management. W praktyce oznacza to identyfikację i redukcję procesów, które generują zbędne koszty, wydłużają czas realizacji i obniżają efektywność operacyjną organizacji. Lean management wyróżnia siedem głównych rodzajów marnotrawstwa, znanych jako muda:
- Jednym z najbardziej kosztownych rodzajów marnotrawstwa jest nadprodukcja, czyli wytwarzanie większej ilości produktów, niż jest aktualnie potrzebne. Prowadzi to do konieczności magazynowania, zwiększonych kosztów operacyjnych i potencjalnego przestarzenia produktów. metody Just-in-Time pozwala na dostosowanie tempa produkcji do rzeczywistego popytu i ograniczenie zbędnych zapasów.
- Oczekiwanie występuje, gdy zasoby, pracownicy lub maszyny pozostają nieaktywne z powodu opóźnień w procesie. Może to wynikać z nieefektywnego harmonogramowania pracy, awarii sprzętu lub niewłaściwego przepływu informacji. Wdrożenie zasad Total Productive Maintenance (TPM) oraz zastosowanie metod zarządzania wizualnego pomagają zminimalizować przestoje i zwiększyć płynność operacji.
- Zbędny transport nie wnosi wartości dodanej i generuje dodatkowe koszty. Może wynikać z nieefektywnego układu przestrzennego zakładu, źle zaplanowanych dostaw czy niewłaściwego rozmieszczenia stanowisk pracy. Optymalizacja układu produkcyjnego i mapowanie strumienia wartości pozwala skrócić dystansów i usprawnić przepływu zasobów.
- Nadmierne zapasy zamrażają kapitał oraz wymagają dodatkowej przestrzeni magazynowej. Zastosowanie m.in. zarządzania zapasami metodą Kanban oraz wdrożenie Just-in-Time pozwala lepiej kontrolować ilość surowców, półproduktów i wyrobów gotowych.
- Nadmierne przetwarzanie to wykonywanie operacji niekoniecznych dla klienta, np. stosowanie nadmiernej jakości czy niepotrzebne formalności administracyjne. Ustandaryzowanie pracy oraz analiza rzeczywistej wartości dla klienta pozwalają wyeliminować zbędne działania.
- Nieefektywne ruchy, czyli zbędne przemieszczanie się pracowników lub ich nieoptymalne działania, powodują straty czasu i energii. Analiza ergonomii pracy, organizacja stanowisk zgodnie z zasadą 5S oraz automatyzacja niektórych operacji zwiększają efektywność operacyjną.
- Wady jakościowe wynikają z błędów, defektów i konieczności poprawek lub ponownej produkcji. Zastosowanie metod takich jak jidoka (autonomizacja), kontrola jakości w czasie rzeczywistym oraz ciągłe doskonalenie (Kaizen, ang. continuous improvement) pozwala na wykrywanie problemów na wczesnym etapie i redukcję kosztów związanych z błędami produkcyjnymi.
Mapowanie strumienia wartości
Kolejną zasadą i jednym z podstawowych narzędzi lean jest mapowanie strumienia wartości (znane też jako Value Stream Mapping). Polega to na analizie wszystkich procesów i etapów, które produkt lub usługa przechodzi od początku do końca. Celem jest pełne zrozumienie, jak wartość jest obecnie tworzona i dostarczana, zidentyfikowanie wszelkiego rodzaju marnotrawstwa oraz obszarów możliwych do poprawy.
Value Stream Mapping służy do wizualizacji przepływu materiałów i informacji w procesach produkcyjnych. Pomaga zidentyfikować marnotrawstwo, niewykorzystany potencjał pracowników, opóźnienia i przestoje , a następnie ulepszyć cały proces produkcji poprzez lepsze planowanie i harmonogramowanie.
Płynny przepływ pracy
Płynny przepływ pracy w koncepcji lean management koncentruje się na optymalizacji sekwencji działań, żeby ograniczyć czas przestojów, kolejek oraz opóźnień w procesach produkcji i operacyjnych. Zapewnia, że każdy etap pracy następuje bez zakłóceń po poprzednim, eliminuje niepotrzebne przerwy oraz nadmierne gromadzenie zapasów czy półproduktów.
Płynność przepływu pracy wspiera system ssący (ang. pull system), który bazuje na rzeczywistym zapotrzebowaniu klienta, co eliminuje konieczność nadmiernej produkcji i przekłada się na zmniejszenie zapasów w zakładach produkcyjnych. Dzięki niemu materiały, komponenty i produkty są dostarczane dokładnie wtedy, gdy są potrzebne.
Równie istotne jest wdrożenie zasady Takt Time, czyli dostosowania tempa produkcji lub świadczenia usług do realnego popytu. Poprzez ustandaryzowanie pracy i eliminację zmienności procesów, organizacje mogą skutecznie unikać nagłych przestojów oraz nierównomiernego obciążenia pracowników, co prowadzi do zwiększenia stabilności operacyjnej i zwiększenie jakości produktów oraz usług.
System ssący
System ssący (ang. pull system) w lean manufacturing to metoda zarządzania przepływem materiałów i produkcji, w której zapotrzebowanie klienta inicjuje działania w łańcuchu dostaw. W przeciwieństwie do tradycyjnego systemu pchającego (push), w którym produkcja odbywa się na podstawie prognoz, system ssący działa na zasadzie rzeczywistego popytu, eliminując nadprodukcję i minimalizując zapasy. Kluczowym narzędziem wspierającym tę koncepcję jest system Kanban, który umożliwia synchronizację dostaw surowców i komponentów z bieżącymi potrzebami produkcji.
W kontekście lean management system ssący przyczynia się do redukcji marnotrawstwa, poprawy płynności operacyjnej linii produkcyjnej i zwiększenia elastyczności całego przedsiębiorstwa, co może być jedną z jego przewag konkurencyjnych. Zapewnia on, że materiały i produkty są dostarczane dokładnie wtedy, gdy są potrzebne, co skutkuje skróceniem czasu realizacji zamówień, lepszym wykorzystaniem zasobów i wysoką jakością produktów.
Kaizen
Kaizen to fundament i jedno z podstawowych narzędzi lean management. Jest to koncepcja zarządzania oparta na kulturze ciągłego doskonalenia procesów, produktów oraz kultury organizacyjnej. Jego istotą jest systematyczne wprowadzanie drobnych, ale regularnych usprawnień, które w długoterminowej perspektywie prowadzą do znaczącej poprawy efektywności operacyjnej. Kaizen zakłada, że każda, nawet najmniejsza zmiana na lepsze, ma wartość i przyczynia się do sukcesu całego przedsiębiorstwa.
W praktyce kaizen promuje aktywne zaangażowanie wszystkich pracowników – od operatorów produkcji po najwyższą kadrę zarządzającą. Kluczowe znaczenie w tym podejściu ma wykorzystywanie wiedzy i doświadczenia osób bezpośrednio zaangażowanych w dany proces, ponieważ to oni najlepiej rozumieją występujące problemy i mogą zaproponować skuteczne rozwiązania.
Podstawowymi narzędziami lean production w kontekście Kaizen są regularne warsztaty i spotkania zespołowe (ang. kaizen events), podczas których analizuje się obszary do poprawy i wdraża konkretne zmiany.
Nieodłącznym elementem tego podejścia jest także szacunek dla ludzi oraz ich rozwój. Organizacje wdrażające tę filozofię inwestują w edukację, szkolenia i empowerment pracowników, umożliwiając im aktywne uczestnictwo w procesie doskonalenia.
Narzędzia lean management
W systemie zarządzania lean wykorzystuje różne praktyczne narzędzia i techniki do poprawy efektywności systemu produkcyjnego, a szerzej także organizacji; oto kilka najważniejszych narzędzi lean:
Metoda 5S
Metoda 5S to jedno z podstawowych praktycznych narzędzi lean management; stosuje się ją, żeby poprawić efektywność operacyjną. Została opracowana w ramach systemu produkcyjnego Toyoty jako sposób na stworzenie uporządkowanego, czystego i ergonomicznego środowiska pracy. Nazwa pochodzi od pięciu japońskich słów zaczynających się na literę “S”, które określają poszczególne etapy wdrożenia:
- Pierwszy krok, Seiri (Sortowanie), polega na przeanalizowaniu wszystkich przedmiotów znajdujących się w miejscu pracy i usunięciu tych, które są zbędne lub nieużywane. Pozwala to skupić się wyłącznie na elementach istotnych dla procesu produkcyjnego lub operacyjnego.
- Kolejnym etapem jest Seiton (Uporządkowanie). W ramach tego kroku stosuje się oznaczenia wizualne, tablice cieniowe oraz system identyfikacji miejsc przechowywania. Dzięki temu operatorzy mogą szybko znaleźć potrzebne narzędzia i materiały.
- Trzecim krokiem jest Seiso (Czyszczenie), który koncentruje się na utrzymaniu czystości w miejscu pracy. Regularne sprzątanie maszyn, stanowisk roboczych i obszarów produkcyjnych nie tylko poprawia bezpieczeństwo, ale także pozwala na wczesne wykrywanie usterek i nieprawidłowości.
- Czwarty etap, Seiketsu (Standaryzacja), polega na ustaleniu i wdrożeniu standardowych procedur dotyczących organizacji miejsca pracy, czyszczenia oraz uporządkowania narzędzi i materiałów. Oznacza to, że wszystkie procesy są jasno określone, powtarzalne i zgodne z najlepszymi praktykami.
- Ostatni krok, Shitsuke (Samodyscyplina), koncentruje się na utrwaleniu nawyków i budowaniu kultury ciągłego doskonalenia. Oznacza to regularne szkolenia pracowników, promowanie odpowiedzialności za utrzymanie porządku oraz zachęcanie do stosowania zasady 5S na co dzień.
Kanban
Tablica Kanban to kolejne narzędzie lean management. Jest to wizualny system do zarządzania pracą w czasie rzeczywistym. Poprzez użycie kart Kanban lub elektronicznych tablic zespoły mogą monitorować postępy, zidentyfikować przestoje i unikać przeciążenia pracy.
Zarządzanie wizualne
Zarządzanie wizualne to metoda organizacji pracy oparta na czytelnych oznaczeniach, wykresach i tablicach informacyjnych, które ułatwiają kontrolę procesów i szybkie podejmowanie decyzji. To narzędzie lean management pomaga usuwać niejasności i usprawnia komunikację w zespole, co zwiększa efektywność operacyjną.
Poka-yoke
Poka-yoke to narzędzie lean management, które pozwala zapobiegać błędom przez zaprojektowanie procesów tak, aby wyeliminować możliwość wystąpienia błędów lub umożliwić ich łatwe wykrycie. Może to obejmować proste urządzenia i alerty, które zapobiegają defektom na etapie produkcji.
Jidoka
Jidoka (automatyzacja z ludzkim dotykiem) to jedno z ciekawszych narzędzi lean management. Oznacza ono dodanie inteligentnej logiki do maszyn, tak aby automatycznie zatrzymywały się w przypadku wystąpienia problemów. Pozwala to na szybką interwencję i zapobieganie produkcji wadliwych części.
Heijunka
Heijunka to praktyka wyrównywania produkcji poprzez stabilizację i standaryzację ilości oraz sekwencji produkowanych elementów. Zapobiega to fluktuacjom i nierównomiernemu obciążeniu w procesach produkcyjnych.
Andon
Andon to wizualny system sygnalizujący status operacyjny i wskazujący problemy w procesie produkcyjnym, co umożliwia szybką reakcję personelu.
SMED (Single-Minute Exchange of Die)
SMED (Single-Minute Exchange of Die) to narzędzie lean stosowane, żeby skrócić czasu przezbrajania maszyn i urządzeń produkcyjnych. Opracowana przez Shigeo Shingo w ramach TPS[8], pozwala ograniczyć czas potrzebny na zmianę narzędzi lub konfigurację linii produkcyjnej do wartości jednocyfrowej, czyli poniżej 10 minut.
Technikę Single-Minute Exchange of Die można podzielić na kilka kluczowych etapów:
- Analiza wszystkich działań wykonywanych podczas przezbrojenia w celu określenia, które z nich można przeprowadzić jeszcze w trakcie pracy maszyny (czynności zewnętrzne), a które wymagają jej zatrzymania (czynności wewnętrzne).
- Maksymalizacja operacji, które mogą być realizowane przed lub po zatrzymaniu maszyny, np. wcześniejsze przygotowanie narzędzi i materiałów, co znacząco skraca czas przestoju.
- Eliminacja zbędnych kroków, uproszczenie procedur, zastosowanie szybkozłączy, systemów samopozycjonujących oraz narzędzi łatwych do wymiany.
- Dokumentowanie i doskonalenie procesu przezbrajania, regularne szkolenie operatorów oraz wdrażanie kolejnych usprawnień w celu dalszej optymalizacji.
Total Productive Maintenance
Total Productive Maintenance (TPM) to narzędzie lean transformation i strategia zarządzania utrzymaniem ruchu, która integruje konserwację maszyn z codziennymi działaniami operacyjnymi. Koncentruje się na eliminacji awarii, zwiększeniu efektywności i zaangażowaniu wszystkich pracowników w utrzymanie sprzętu. Zapewnia stabilność procesów, redukując przestoje i poprawiając jakość produkcji.
Six Sigma
Six Sigma w kontekście narzędzi lean management może być uzupełniającą metodologią, skoncentrowaną na redukcji zmienności procesów i eliminacji defektów, co pozwala na osiągnięcie stabilnej i wysokiej jakości produkcji. Integracja pozostałych narzędzi lean management z metodologią Six Sigma prowadzi do synergii, łącząc eliminację marnotrawstwa z precyzyjną analizą danych i statystyczną kontrolą procesów.
Wdrażanie lean management
Przebieg wdrażania lean management w firmie rozpoczyna się od dokładnej analizy aktualnego stanu przedsiębiorstwa, identyfikacji głównych problemów operacyjnych oraz określenia kluczowych obszarów wymagających usprawnień. Konieczne jest precyzyjne zrozumienie wartości z perspektywy klienta, aby ukierunkować działania na zwiększenie efektywności procesów.
Pierwszym etapem wdrożenia jest mapowanie strumienia wartości, czyli szczegółowa analiza wszystkich etapów produkcji lub świadczenia usług. Celem tego działania jest identyfikacja operacji, które nie przynoszą wartości dodanej, oraz wskazanie obszarów, w których występują nieefektywności, takie jak nadprodukcja, zbędne zapasy, niepotrzebne przestoje czy nadmierny transport. Na podstawie tej analizy opracowywane są konkretne usprawnienia, które pozwolą na eliminację strat i zwiększenie płynności procesów.
Następnym krokiem jest wdrożenie koncepcji przepływu, polegającej na optymalizacji sekwencji działań w celu zapewnienia nieprzerwanego i płynnego funkcjonowania procesów. W tym kontekście szczególne znaczenie ma zastosowanie narzędzi lean management, takich jak system pull, który minimalizuje nadmierne zapasy i redukuje czas realizacji zamówień.
Ważnym elementem wdrożenia jest zaangażowanie pracowników i budowanie kultury ciągłego doskonalenia, znanej jako Kaizen. Sukces zastosowania koncepcji i narzędzi lean management zależy od aktywnego udziału zespołów operacyjnych w identyfikowaniu problemów i proponowaniu usprawnień. W tym celu organizowane są szkolenia, warsztaty oraz systemy zgłaszania pomysłów, które pozwalają pracownikom na bieżąco wdrażać zmiany i monitorować ich skuteczność.
Ostatnim etapem jest wdrożenie systemu monitorowania i oceny wyników. Regularne pomiary efektywności procesów, analiza KPI oraz cykliczne audyty narzędzi lean management i wpływu ich stosowania na efektywność organizacji pozwalają dynamicznie reagować na nowe wyzwania, utrzymywać wysoki poziom efektywności operacyjnej i zapewniać klientom produkty oraz usługi o najwyższej jakości.
Zastosowania lean management
Koncepcję i narzędzia lean management stosuje się w różnych sektorach gospodarki:
Przemysł produkcyjny
W przedsiębiorstwach produkcyjnych lean management jest stosowany do optymalizacji procesów wytwórczych, skracania czasów cykli produkcyjnych oraz redukcji kosztów operacyjnych. Metody takie jak Just-in-Time (JIT) czy Total Productive Maintenance (TPM) pozwalają na ograniczenie nadmiernych zapasów, zwiększenie jakości produktów oraz zwiększenie dostępności maszyn i urządzeń. Przykładami firm z tego obszaru, które stosują narzędzia lean management są:
- Toyota jest często uważana za prekursora lean management dzięki swojemu systemowi produkcyjnemu (Toyota Production System). Metody i narzędzia lean pozwoliły Toyocie stać się jednym z największych i najbardziej efektywnych producentów samochodów na świecie[9].
- Boeing, jeden z przodujących producentów w przemyśle lotniczym, zaadoptował lean manufacturing w celu zmniejszenia czasu produkcji i kosztów, jednocześnie zwiększając jakość swoich produktów[10].
Logistyka i zarządzanie
W logistyce i zarządzaniu łańcuchem dostaw lean management pozwala na optymalizację procesów transportowych, magazynowania oraz dystrybucji. Poprzez wdrożenie systemu ssącego (pull system) oraz standaryzację operacji można zminimalizować czas dostaw i uniknąć nadmiernych zapasów. Przykładowo Nike wdrożyło lean manufacturing w swojej sieci dostaw, skutecznie zmniejszając czas i koszty produkcji, jednocześnie zwiększając reakcję na zmieniające się trendy rynkowe[11]. Implementacja lean pomogła również firmie w skuteczniejszym zarządzaniu zasobami i zrównoważeniu produkcji.
Usługi
W sektorze usług lean management przyczynia się do poprawy jakości obsługi klienta oraz optymalizacji procesów administracyjnych. Banki, firmy ubezpieczeniowe czy centra usług wspólnych wdrażają metody eliminacji zbędnych procedur, redukcji czasu oczekiwania oraz standaryzacji pracy, co prowadzi do większej efektywności operacyjnej. Zastosowanie technik lean w usługach pozwala na uproszczenie procesów, zmniejszenie biurokracji oraz poprawę satysfakcji klientów.
E-commerce
Lean management w e-commerce koncentruje się na optymalizacji procesów logistycznych, eliminacji marnotrawstwa i poprawie doświadczeń klientów. Przykładem jest Amazon, sklep internetowy i firm technologiczna, który z powodzeniem zastosował zasady lean management w swoich centrach logistycznych[12]. Techniki takie jak 5S, Kaizen, i JIT pozwalają szybko i skutecznie reagować na potrzeby klientów, co jest szczególnie ważne w dynamicznym świecie e-commerce.
IT i rozwój oprogramowania
W branży IT i rozwoju oprogramowania lean management znajduje zastosowanie w metodykach zwinnych, takich jak Agile czy DevOps. Dzięki koncepcji ciągłego doskonalenia i optymalizacji przepływu pracy zespoły programistyczne mogą szybciej dostarczać produkty, minimalizować błędy oraz elastycznie dostosowywać rozwiązania do zmieniających się wymagań rynkowych. Przykładem jest Intel wdrożył zasady lean manufacturing w swoich procesach produkcyjnych, dzięki czemu skrócił czas cyklu, zwiększył jakość i zmniejszył koszty[13]. Wprowadzenie kultury ciągłego doskonalenia pozwoliło pracownikom na aktywny udział w usprawnianiu procesów.
Sektor budowlany
W sektorze budowlanym lean manufacturing pozwala optymalizować harmonogramy prac, redukować straty materiałowe oraz efektywniej zarządzać projektami. Zastosowanie zasad lean w budownictwie prowadzi do skrócenia czasu realizacji inwestycji, eliminacji przestojów oraz lepszego wykorzystania zasobów ludzkich i technicznych.
Administracja publiczna
Lean management znajduje również zastosowanie w administracji publicznej, gdzie jego wdrożenie pozwala na poprawę efektywności procesów urzędowych, redukcję biurokracji oraz zwiększenie transparentności działań. Dzięki standaryzacji procedur i optymalizacji pracy urzędnicy mogą skuteczniej obsługiwać obywateli, zmniejszając liczbę zbędnych formalności oraz skracając czas realizacji spraw.
Ograniczenia lean management
Jednym z kluczowych wyzwań metody lean jest trudność w pełnej eliminacji marnotrawstwa. Procesy optymalizacyjne wymagają ciągłej analizy i doskonalenia, więc osiągnięcie stanu całkowitej efektywności jest praktycznie niemożliwe.
Lean management zakłada aktywne uczestnictwo wszystkich członków organizacji w identyfikacji i eliminacji strat, co wymaga zmiany mentalności oraz długofalowego budowania kultury ciągłego doskonalenia. Brak odpowiedniego zaangażowania ze strony kadry zarządzającej lub pracowników może prowadzić do powierzchownego wdrożenia metod lean.
Firmy wdrażające tę metodologię często dążą do minimalizacji zapasów i optymalizacji przepływu pracy, co może zwiększyć podatność na zakłócenia w łańcuchu dostaw, problemy z nieoczekiwanym wzrostem popytu lub utrudnienia w przypadku nieprzewidzianych awarii maszyn i urządzeń.
Wdrożenie filozofii lean wymaga nie tylko zmian strukturalnych, ale także zmiany sposobu myślenia i działania pracowników na wszystkich szczeblach organizacji. Osiągnięcie wymiernych rezultatów może zająć wiele miesięcy lub lat, co dla firm oczekujących szybkich efektów może stanowić barierę.
Sektory, w których występuje duża niepewność, krótkie serie produkcyjne lub częste zmiany w specyfikacji produktów, mogą mieć trudności z pełnym wykorzystaniem tej metodologii. W takich przypadkach większą efektywność mogą zapewnić inne podejścia, takie jak Agile czy Six Sigma.
Korzyści z lean management
Wdrożenie lean management przynosi szereg korzyści, które wywierają przemożny wpływ na różne aspekty działalności organizacji. Na pierwszy plan wysuwa się zwiększenie efektywności poprzez eliminację marnotrawstwa w procesach, dzięki czemu organizacje mogą lepiej wykorzystać zasoby, zapewniając sobie tym samym niższe koszty operacyjne. Przekłada się to także na poprawę jakości produktów i usług. Pracownicy zaangażowani w poszukiwanie sposobów na usprawnienie procesów i eliminację defektów przyczyniają się do naturalnego wzrostu jakości, a zatem również większego zadowolenia klientów.
Lean management promuje kulturę organizacyjną stawiającą na ciągłe doskonalenie i zachęca pracowników na wszystkich szczeblach do udziału w innowacji i doskonaleniu. Tworzy to środowisko pracy, w którym wszyscy członkowie zespołu czują się wartościowi i wiedzą, że ich głos ma znaczenie, co przekłada się na większe zaangażowanie i satysfakcję z pracy.
W miarę upływu czasu rośnie także elastyczność i szybkość reakcji na zmiany na rynku lub potrzeby klientów – skrócenie czasu cyklu produkcji i dostaw pozwala szybciej reagować na zmieniające się warunki. Wszystkie wymienione korzyści tworzą silniejszą, bardziej konkurencyjną organizację i składają się na model biznesowy, który może wytrzymać próbę czasu i zapewnić trwały sukces na rynku.
FAQ
Przypisy
Formularz kontaktowy
Rozwijaj swoją firmę
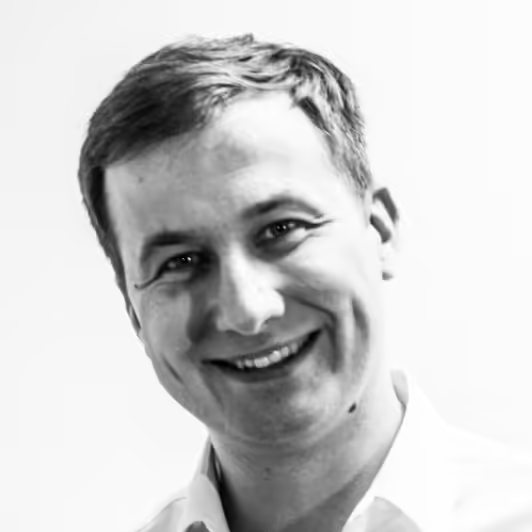
Zajmuję się sprzedażą i pielęgnacją relacji z klientami. Codziennie dbam o to, żeby nasi partnerzy biznesowi otrzymywali wsparcie najwyższej jakości oraz pomagam im w realizacji ich celów biznesowych – sukces naszych klientów jest naszym sukcesem.
Oceń tekst
Być może zainteresują Cię:
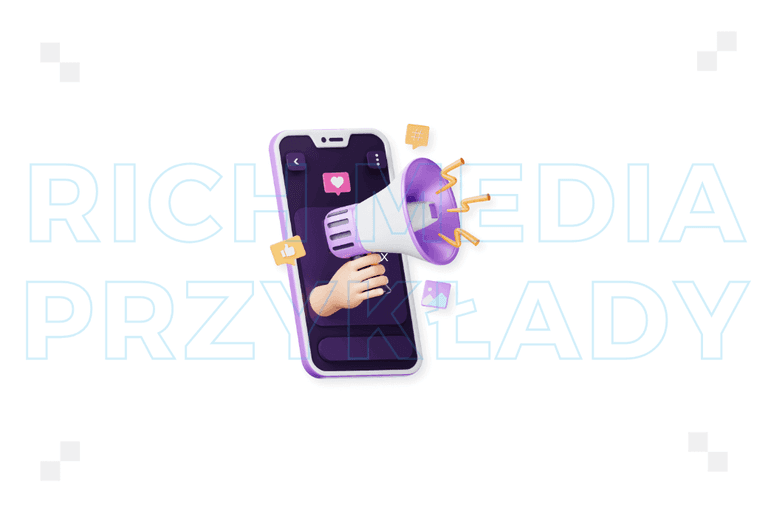
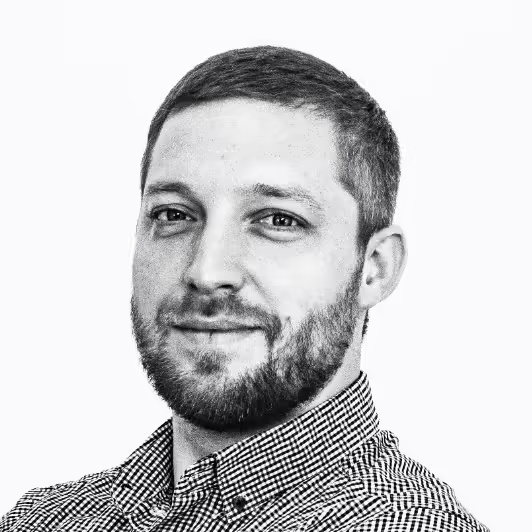
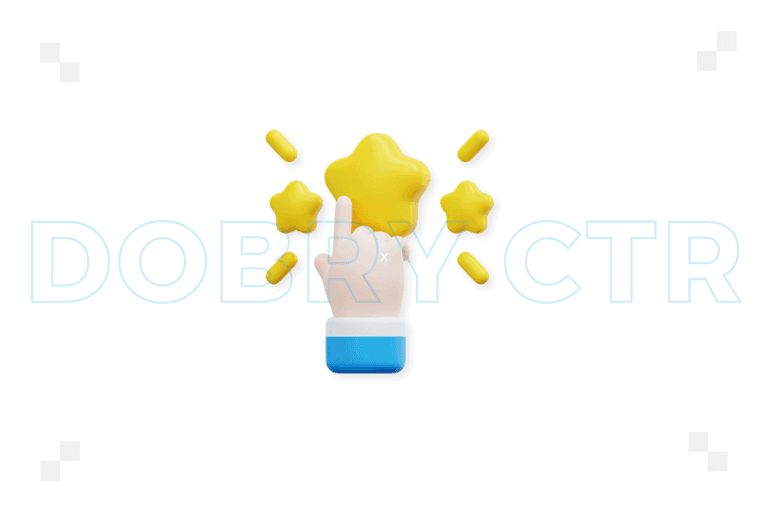
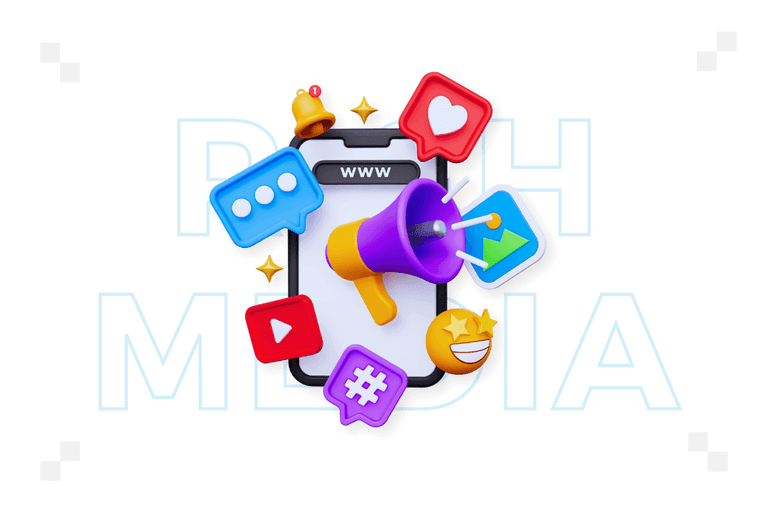