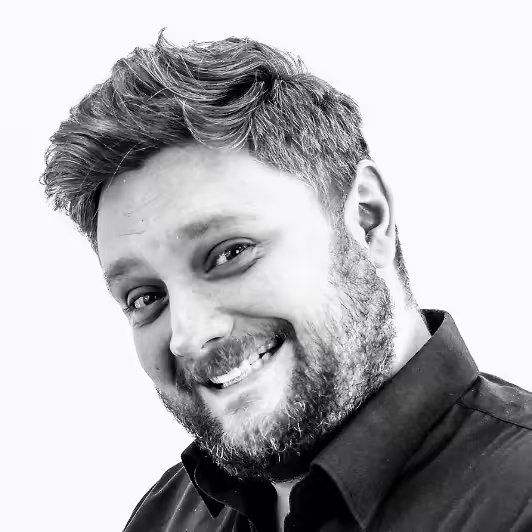
Ishikawa diagram – what it is, examples of use
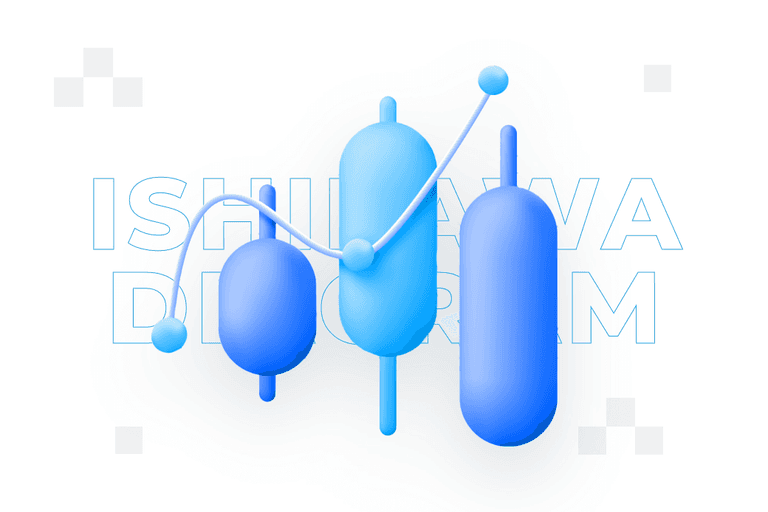
An Ishikawa chart is a tool that enables professionals in various industries to analyse and solve complex problems. How do you create it and where does it find use?
In this article you will find out:
- What is an Ishikawa chart?
- What types of Ishikawa diagrams are there?
- How to build an Ishikawa chart?
- What are some examples of applications of an Ishikawa chart?
- What are the limitations of an Ishikawa chart?
- What can be gained from an Ishikawa chart?
Ishikawa chart – definition
An Ishikawa chart, also known as a fishbone diagram, is an analysis tool used to understand the causes of various problems, especially in the context of quality control and process management. Its name comes from a Japanese quality management engineer, Kaoru Ishikawa, who developed it in 1968. In the following years, the diagram became part of a wider methodology known as Total Quality Management (TQM), which developed in Japan, mainly in the automotive and manufacturing industries after World War II.
The history of the Ishikawa diagram is closely linked to the development of quality management practices in Japan in the post-war period. Kaoru Ishikawa, while working on ways to improve quality in Japanese industry, was inspired by the earlier work of experts such as W. Edwards Deming. His contributions helped Japanese companies achieve world-class standards of quality and productivity, contributing to Japan’s economic miracle in the post-war years.
The Ishikawa chart helps teams to focus on identifying the root causes of a problem, and its graphical representation allows them to understand the sources more quickly. The central element of the chart is the specific problem, often written at the right end of the main horizontal arrow (or ‘spine’). It is led by a series of diagonal lines (‘bones’) on which teams record the potential causes of the problem.
An Ishikawa chart is a visual tool used to identify, track and analyse the potential causes of a particular problem in a process or system.
Definition of an Ishikawa chart
Each category is analysed in terms of how it may contribute to the root problem. The causes are often broken down further into more specific factors, and when creating an Ishikawa chart, group brainstorming is often used. This allows different perspectives and experiences to be brought together, resulting in a more comprehensive understanding of the causes of the problem.
Types of Ishikawa diagram
The Ishikawa diagram, although mainly known for its single format (fishbone diagram), can be modified or used in different ways depending on the specific problem, industry or team preference. Choosing the right type depends on the specific problem the organisation is experiencing and the industry in which it operates. It is important for teams to choose the model that best suits their specific analytical and operational needs. Here are the most commonly used options:
Standard Ishikawa chart (6M)
This is the most common form, in which the ‘bones’ are divided according to six categories, called 6M: methods, machines, people (English for ‘manpower’), materials, environment (English for ‘mother nature’) and measurement (English for ‘measurement’). Each category is explored to understand how it might contribute to the problem.
The 8M diagram
This is an extension of the standard 6M model with two additional categories: ‘management’ (from ‘management’) and ‘maintenance’ (from ‘maintenance’). It is often used in more complex industrial environments where the additional categories have a significant impact on process outcomes.
The 4M1D chart
Focuses on four categories: machines, materials, methods and people (from English ‘manpower’), with ‘defects’ as the focal point of analysis. The team starts with a specific defect or error and analyses how the 4M factors may be contributing to it.
5W1H diagram
Uses a methodology based on the questions who (‘who’), what (‘what’), when (‘when’), where (‘where’), why (‘why’) and how (‘how’). This is particularly useful when the cause of a problem is not clear and the team needs to conduct an in-depth investigation to get to the root of the problem.
Building an Ishikawa diagram
The construction of an Ishikawa diagram starts with defining the problem around which the whole analysis will be focused. It should be clear and as specific as possible so that all team members can understand it. It is often advisable to present the problem in the form of a question, for example, “Why did our production decline in the last quarter?”.
We then draw a straight horizontal line in the middle of a sheet of paper or whiteboard – this will be the ‘spine’ of our fish, representing the main sequence of the process or problem. At the end of this line, we write down the problem we defined earlier in a rectangle or oval, representing the ‘head’ of the fish. Now the brainstorming begins, in which participants will identify the main categories of causes that can influence the problem – these will become the main ‘bones’ in the fishbone diagram.
We draw each of the main categories of causes as lines extending at an angle from the main spine, creating a structure resembling a fishbone. It is important not to go too deeply into detail at this stage; the main aim is to establish broad categories. You then return to brainstorming, but this time you need to focus on the more detailed causes within each of the main categories – adding them as smaller ‘bones’ to the corresponding larger ‘bones’. The process continues until the ideas are exhausted. At the same time, it is important to note that some causes may be related or influence other factors – dependencies also need to be included in the diagram, which may require the addition of lines connecting different elements or subgroups of causes.
The final step is to analyse and revise the diagram. The team should critically evaluate the diagram, making sure that all possible causes are included and that the structure makes sense. This may sometimes require additional research or data to confirm whether the reported causes are real. Once completed, the Ishikawa chart serves as a roadmap for further investigation, testing solutions and implementing changes.
Examples of the use of an Ishikawa chart
The Ishikawa chart is applicable in a wide variety of situations. Its versatility and ability to unmask the root of problems make it the preferred tool for professionals seeking continuous improvement and efficiency in many areas:
- A manufacturing company may have a problem with defects in finished products. An Ishikawa chart can help identify possible causes, such as improper materials, outdated machinery, human error in the production process, inconsistent working methods or quality control problems. Based on this, a company can, for example, improve employee training, update equipment or introduce new quality control protocols.
- A hospital struggling with a high rate of nosocomial infections can use an Ishikawa chart to examine aspects of care that may be contributing to the problem. These can include hygiene procedures, visiting policies, antibiotic use, medical equipment and even staff culture. With this, the hospital can begin to work on reducing the risk of infection through, for example, infection control training, changes to cleaning protocols or improved communication within teams.
- An internet services company that experiences a high number of reports of network outages can use the Ishikawa chart to identify the root of the problem and, based on this, decide, for example, to update its equipment, improve its outage response procedures or increase bandwidth to better meet user demand.
Limitations of an Ishikawa chart
One of the main limitations of the Ishikawa diagram is that, while the diagram can effectively indicate the various potential causes of a problem, it does not indicate which is the most significant. This means that teams may need additional statistical or analytical tools to understand exactly which factors most influenced an issue. In addition, it relies on the knowledge and experience of those creating the diagram, so if team members do not have sufficient knowledge of the process or issue, they may overlook key causes.
Another limitation is the lack of clear solutions or indications of a course of action. An Ishikawa diagram helps to identify potential causes, but determining the most effective methods to fix the problem often requires additional analysis and evaluation. There is also a risk that placing too much emphasis on identifying causes within internal processes and systems may divert attention from external factors that may have just as much influence on the problem. Changes in the market environment or consumer behaviour are often difficult to capture in the structure of an Ishikawa chart, but can greatly affect the performance of an organisation. An Ishikawa chart may also not reflect changes over time, meaning that the causes identified at the start of the analysis may change.
Benefits of an Ishikawa chart
An Ishikawa chart promotes a holistic approach to a problem – rather than focusing on a single cause, it allows teams to carefully examine a wide range of potential factors that may be contributing to a problem. This includes both immediate and more subtle factors, which helps prevent superficial or hasty conclusions.
At the same time, the chart facilitates collaboration, as people from different departments or with different specialisms are often involved in charting. This allows teams to better understand how different aspects of the organisation affect each other, as well as identifying issues that may have been overlooked in a narrower study.
An Ishikawa diagram is also a valuable communication tool, and its visual nature helps to ensure that all members understand the problem. It also makes it easier to present the problem and its potential causes to those outside the team, such as stakeholders or customers, providing a clear picture of the situation.
By requiring teams to identify different causes of a problem, the Ishikawa diagram stimulates creative thinking and encourages the search for innovative solutions. This can lead to the discovery of new ways of approaching work that might have been overlooked in more traditional forms of analysis. It can also be a fundamental part of improving organisational culture in a company by regularly assessing and identifying areas for improvement.
FAQ
Contact form
Develop your brand
Rate content:
You may be interested in:
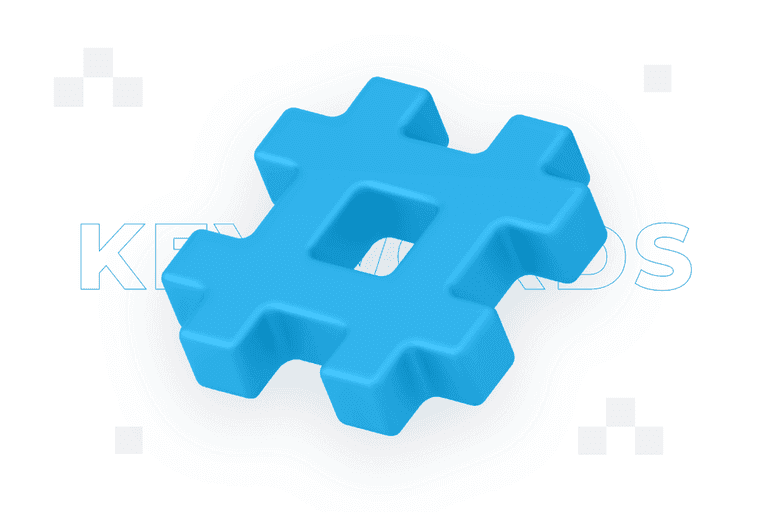
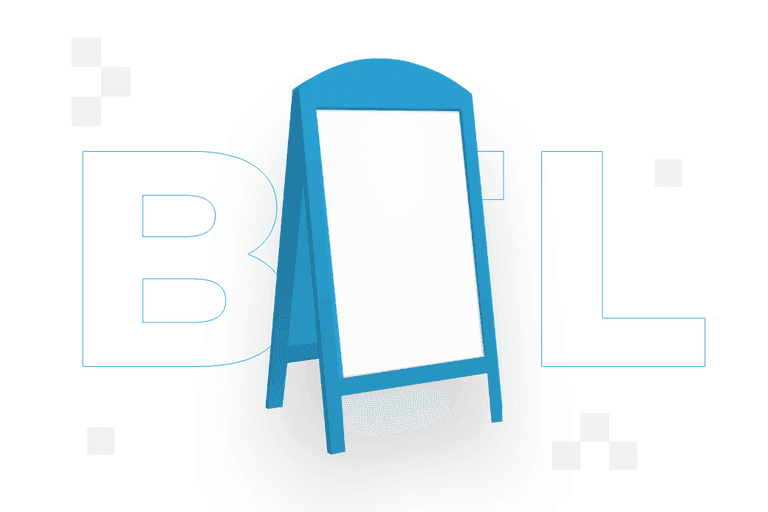
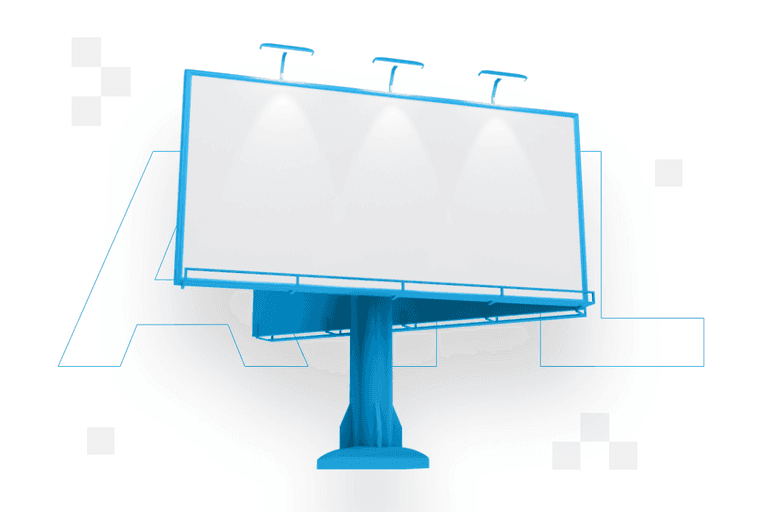